Artykuł sponsorowany
Jakie są zastosowania elektrodrążenia w precyzyjnej obróbce metali?
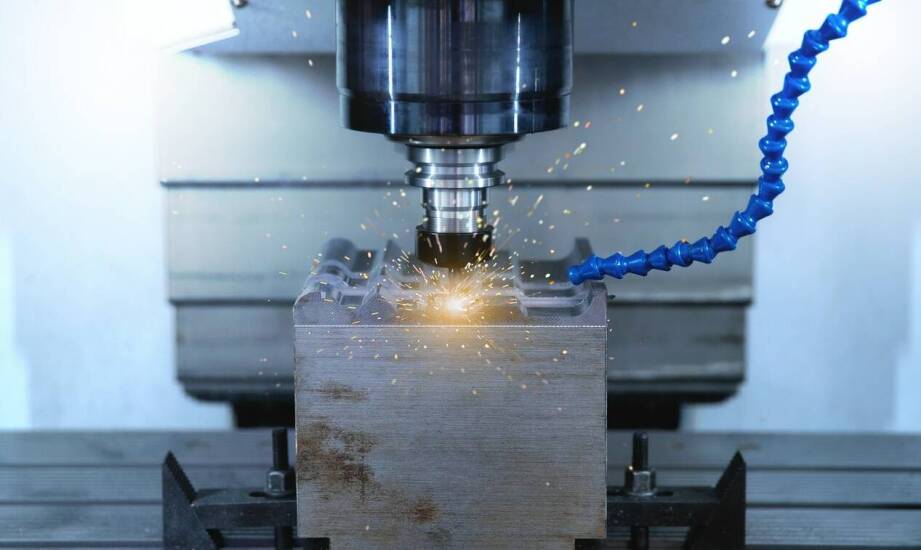
Elektrodrążenie to nowoczesna metoda obróbki metali, która zyskuje popularność w przemyśle. Wykorzystując prąd elektryczny, umożliwia precyzyjne usuwanie materiału, co jest szczególnie przydatne w obróbce metali trudnoobrabialnych. Artykuł przedstawia zasady działania tej technologii, jej zastosowania, korzyści oraz wyzwania z nią związane. Warto zauważyć, że elektrodrążenie znajduje zastosowanie w wielu branżach, takich jak motoryzacja czy lotnictwo. Dzięki tej metodzie możliwe jest uzyskanie skomplikowanych kształtów i detali, które są trudne do osiągnięcia tradycyjnymi sposobami obróbczych.
Elektrodrążenie metali trudnoobrabialnych
Proces ten ma istotne znaczenie dla materiałów takich jak tytan czy stopy niklu. Charakteryzują się one wysoką wytrzymałością i odpornością na korozję, co utrudnia ich obróbkę tradycyjnymi metodami. Elektrodrążenie pozwala na precyzyjne usunięcie materiału bez stosowania siły mechanicznej, co minimalizuje ryzyko uszkodzenia struktur. Dzięki temu można uzyskać skomplikowane kształty i detale, czyniąc tę technologię kluczowym narzędziem w produkcji komponentów dla przemysłu kosmicznego, energetycznego oraz chemicznego.
Precyzyjność i złożoność kształtów
Precyzyjność oraz złożoność uzyskiwanych dzięki elektrodrążeniu kształtów sprawiają, że technologia ta jest niezastąpiona w wielu branżach. Umożliwia tworzenie cienkich i skomplikowanych struktur wymagających dużej dokładności. Proces ten pozwala na wykonanie precyzyjnych otworów o średnicach kilku mikrometrów oraz kształtowanie złożonych powierzchni. Jest szczególnie przydatny w produkcji części dla przemysłu medycznego, lotniczego i elektronicznego, gdzie wymagana jest wysoka jakość wykonania.
Wymagania techniczne i kwalifikacje
Aby skutecznie stosować elektrodrążenie, należy spełnić określone wymagania techniczne oraz posiadać odpowiednie kwalifikacje. Niezbędne są maszyny do elektrodrążenia o wysokiej precyzji, a także specjalistyczne elektrody i płyny dielektryczne. Pracownicy muszą mieć doświadczenie w obsłudze tych urządzeń oraz znajomość zasad działania tej technologii. Wiedza o materiałach i ich właściwościach jest kluczowa dla wyboru odpowiednich parametrów procesu.
Wyzwania i ograniczenia elektrodrążenia
Mimo zalet, elektrodrążenie wiąże się z wyzwaniami i ograniczeniami. Kluczowe jest precyzyjne dobieranie parametrów procesu, co wpływa na jakość finalnego produktu. Obróbka może być czasochłonna, zwłaszcza przy trudnych materiałach. Zużycie elektrod wymaga regularnej wymiany, a utrzymanie odpowiednich warunków pracy maszyn jest niezbędne. Nieprawidłowa eksploatacja może prowadzić do uszkodzeń sprzętu.